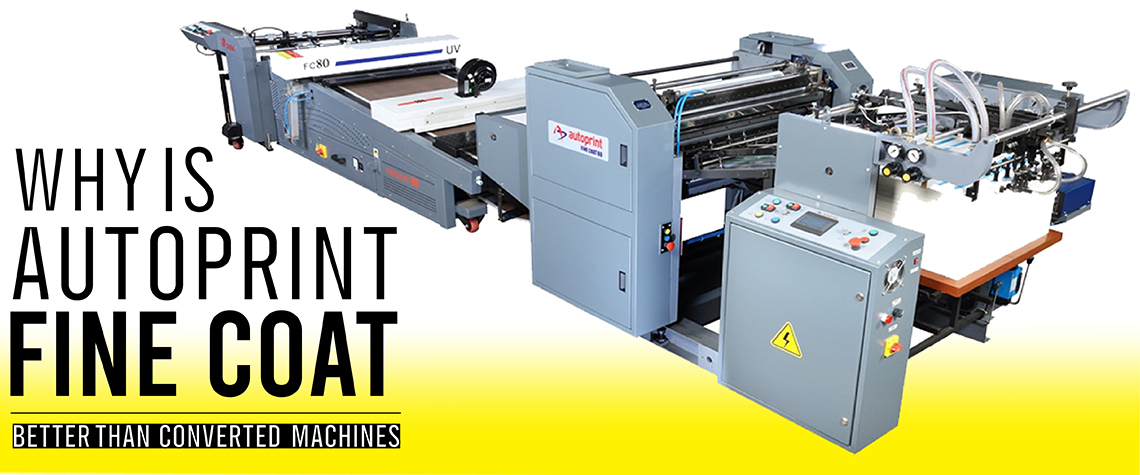
19-07-2021 | AUTOPRINT
Let’s get to know about the difference and the band new machines and the converted machines. Brand new Autoprint machines are manufactured to perform a particular job effectively and precisely. But whereas the other converted machines are made for other purposes and after some years of use it’s been attached with some other machine to give a different end product
The main disadvantage is of the converted machines are that they are already been used for 10-15 years and been attached to another machine to run the job. Basically the same brand will not be attached together as converted machine, both different brands will be fit to perform the job here the actual problem starts. The alignment of the machines are been changed as they are fit to totally different brands.
E.g.: X brand for printing + Y brand for UV coating
If any one of the spares goes repair, the spares can’t be got from anywhere because they are very old machines and may be they can be recreated using a local moulding factories but never the Duplicate becomes the Original.
There are some comparisons given below for your easy understanding
Autoprint Brand:
- All parts of Autoprint which are in contact with coating are made of hard chrome plating or stainless steel
- Two sets of cleaning systems/tray provided so that switch between aqueous and UV can be done very quickly (within 10 minutes)
- 3 roller anilox system gives best quality of coating in print industry
- Coating thickness can be controlled by 3 roller system by adjusting the intermediate pressure and also by changing the anilox roller
- 25% less consumption in spot not coating,25 % cheaper on coatings as this coating is less expensive as special coating is not required to be used.(Total 50% less)
- Inventory cost on raw material ie very less
Converted machines:
- Contact parts with varnish are not made of stainless steel as initially designed for printing may lead faster wear and tear
- It takes more time as whole system needs cleaning and additional tray is not provided. This adds more time for change over(15min on each job change)
- normally a two roller system or a single roller system with anilox is used which does not give the best result
- Cannot be adjusted and only gives fixed out flow. For coating thickness change, anilox roller need to be replaced
- Not possible to do spot not coating. If such a job is coated then we have to use a coating on which ink jet will adhere. This makes the coating at least 25% more expensive, other than the area coated, as full area will only be coated.
- Need to store more film in various sizes & glue
So it’s always the best to choose the new machine to the converted machine, as they are one time investment and life time profit.